„Green Fabrics“ – wie aus Abfällen wahre Schätze werden
PET-Filz – ein 100% recyclebares Formvlies
Umweltfreundlich, funktionell, schallabsorbierend, weich im Griff, vielseitig einsetzbar… Es gibt unzählig viele Eigenschaften, die man dem Stoff PET-Filz zuschreibt. Kein Wunder, dass das Material immer beliebter wird. Es kombiniert ein nachhaltiges Design mit einer großen Auswahl an Farben und Fähigkeiten. In Deckenelemente, Wandverkleidungen, Trennwände und in Beleuchtungen kommt das Material schon länger zum Einsatz – aber auch die Möbelindustrie hat den Werkstoff für sich entdeckt.
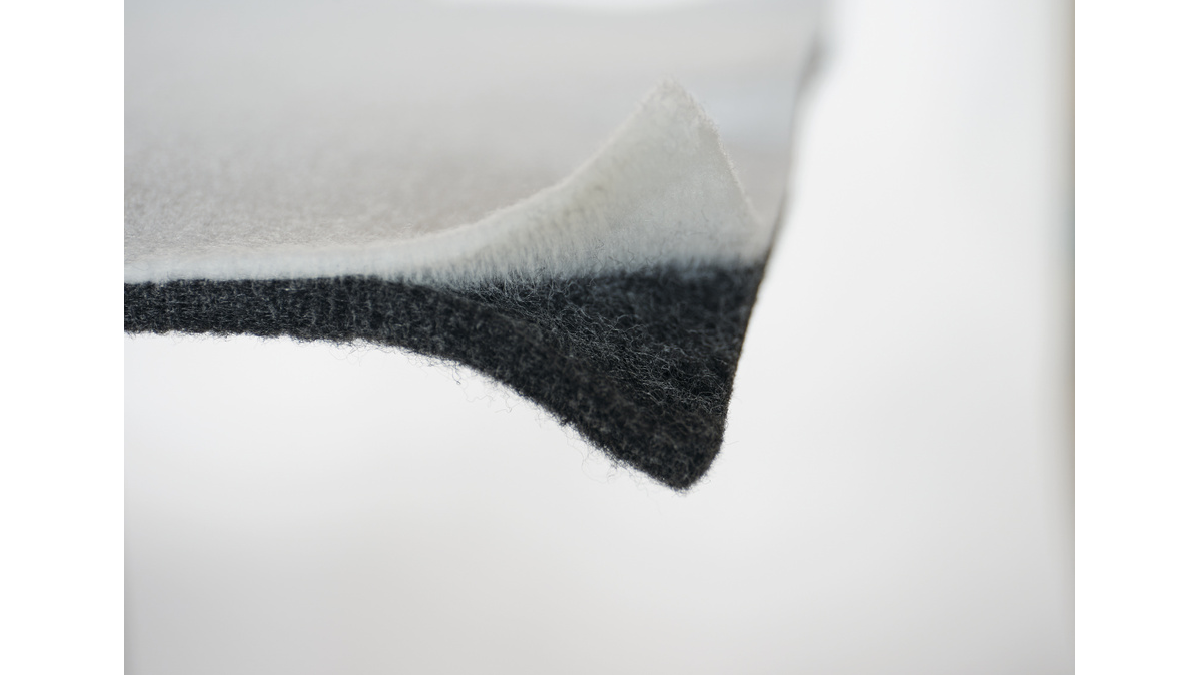
PET-Filz (Polyethylenterephthalat) wird aus recycelten Plastikflaschen hergestellt. Das Filzmaterial kann nach der Verwendung wiederverwendet oder recycelt werden, wodurch sich die Lebensdauer des Werkstoffes über seine ursprüngliche Verwendung hinaus erheblich verlängert. Copyright: Klöber
Der deutsche Sitzmöbelhersteller Klöber hat eine ganze Produktfamilie mit PET-Filz auf den Markt gebracht. Bei WOOOM ist die Sitzschale des Loungesessels, des niedrigen Schalensessels und des Besprechungsstuhls aus Formvlies. „Nachhaltigkeit ist für uns kein Megatrend, sondern eine Selbstverständlichkeit“, sagt Thomas Möller, Geschäftsführer von Klöber. „Bei jeder neuen Entwicklung streben wir danach, den Anteil neuer Rohstoffe auf das Nötigste zu senken und setzen stattdessen so viel hochwertiges Recyclingmaterial ein wie möglich. PET-Filz wird aus recycelten Plastikflaschen hergestellt. Mit einem fast unendlichen Vorrat an wiederverwendbaren Materialien stellen PET-Filzstoffe einen wichtigen Schritt dar, um Einweg-Plastikflaschen aus Mülldeponien und Ozeanen zu verbannen. Die Verwendung des Werkstoffs löst sicherlich nicht das Problem, aber wir leisten einen kleinen Beitrag, auf den wir stolz sind.“
PET-Filz ist zu 100 % recycelbar. Es enthält bis zu 60 % wiedergewonnene Polyesterfasern aus sogenannten Bottle Flakes, d.h. geschredderten PET-Flaschen, die bei Klöber zu 100% aus europäischen Regionen stammen.
Leap – ein Lederimitat aus Apfelresten
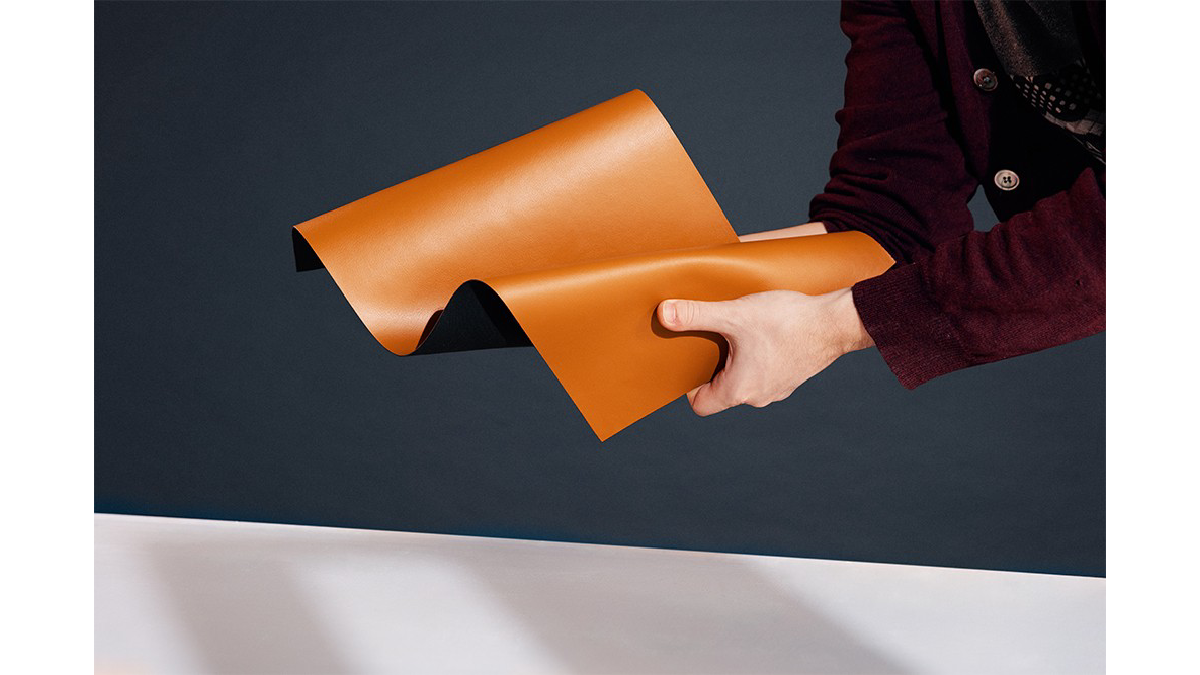
Leap ist die Abkürzung für „LEftover APples“. Es ist ein vegan-zertifizierter Werkstoff der nächsten Generation mit einem Anteil von 89 % an biobasiertem Material. Copyright: Beyond Leather Materials
Ein Apfel ist ein beliebter Snack für zwischendurch: Die Frucht passt in fast jede Tasche, ist leicht zu essen und auch noch gesund. Während rund 75% der weltweiten Apfelernte direkt verzehrt werden, werden etwa 25% zu Saft, Marmelade und anderen Lebensmittel weiterverarbeitet. Es wird geschätzt, dass dabei jedes Jahr rund 3.000.000 Tonnen Apfelreste anfallen, die im Müll laden. Ein Zustand, den das dänische Start-up Beyond Leather Materials untragbar findet. Aber was kann man mit Apfelresten machen? Ein Lederimitat!
Die erste Idee war schnell geboren. Der Weg zum finalen Produkt war aber mühsam. Gemeinsam mit Ingenieurinnen und Ingenieuren von KEA entwickelte das Team von Beyond Leather Materials einen lederartigen Stoff und nannten ihn Leap, abgeleitet von „LEftover Apples“. Leap besteht aus aufbereiteten Apfelabfällen, Naturkautschuk und anderen biobasierten Inhaltsstoffen. „Durch die Verwendung von Apfelmark wollen wir einen positiven Beitrag leisten, indem wir den Apfelsaft- und Apfelweinproduzenten helfen, ihre Abfallkosten zu senken und verhindern, dass Äpfel auf Mülldeponien landen“, erklärt Mikael Eydt, Co-Founder und CEO von Beyond Leather Materials. „Dieser Ansatz ermöglicht es uns, eine innovative Alternative zu Materialien auf Tierbasis zu schaffen.“
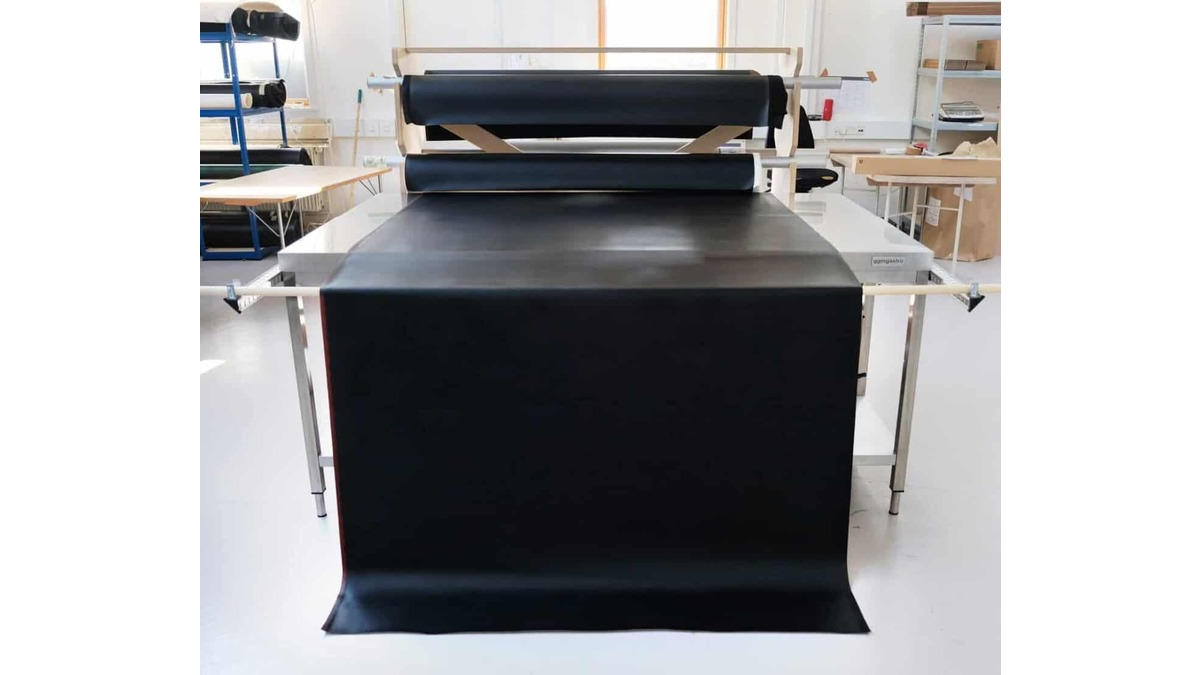
Wichtiger Schritt nach vorne: Im Mai 2024 hat das Team von Beyond Leather Materials die erste vollwertige Rolle-zu-Rolle-Produktionslinie in Deutschland in Betrieb genommen. Copyright: Beyond Leather Materials
Zuletzt hat Beyond Leather Materials einen wichtigen Schritt nach vorne gemacht: Im Mai 2024 hat das Team die erste vollwertige Rolle-zu-Rolle-Produktionslinie in Deutschland in Betrieb genommen. „Fast sieben Jahre Produktentwicklung und intensive Forschung haben uns zu diesem entscheidenden Moment geführt“, sagt Eydt. „Leap steht für einen Wandel in der Art und Weise, wie wir Abfälle betrachten und nutzen, und verwandelt ausrangierte Materialien in wertvolle Ressourcen. Das Produkt ist ein Beispiel dafür, wie wir in Branchen, die oft auf tierische Materialien oder reine Kunststoffe angewiesen sind, einen Schritt weiter in Richtung eines durchdachteren Ansatzes bei der Materialnutzung gehen können.“
Sealwool – ein Garn aus Austernschalen
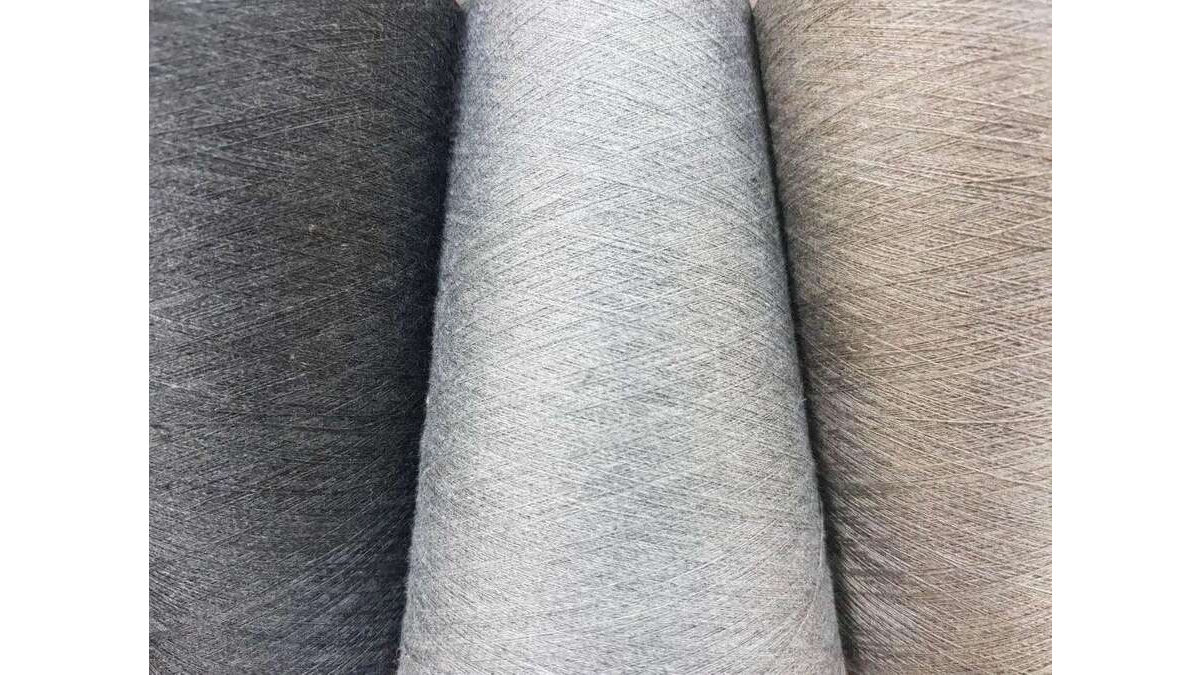
Seawool ist das neueste nachhaltige Garn, das von Creative Tech Textile entwickelt und zusammen mit Hans Global in den internationalen Markt eingeführt wurde. Copyright: Creative Tech Textile
Die Austernzucht hat in Taiwan eine lange Tradition. Seit über 300 Jahren „produziert“ das Land Austern in Hülle und Fülle. Dass durch die Abfälle, die Austernschalen, allerdings ein unterschätztes Müllproblem entsteht, da die Schalen nicht verrotten, wurde jahrelang übersehen. Allein in Taiwan fällt durch die Zucht mehr als 160.000 Tonnen Schalenabfall jährlich an. Obwohl einige der Austernschalen zu Bodenverbesserungen oder Lebensmittelpellets für Nutztiere verwendet werden, wurde das Problem nicht gelöst.
Nach jahrelanger Forschung ist es Creative Tech Textile nun gelungen, eine Methode zu entwickeln, um aus den weggeworfenen Muschelschalen ein Garn zu spinnen: Seawool. In einer Fabrik werden die Schalen zu Nanoperlen gemahlen und mit Garn aus recycelten Plastikflaschen kombiniert. Am Ende der Produktion entsteht ein Material, das über die natürlichen Eigenschaften weggeworfener Austernschalen verfügt. Es hat einen wollähnlichen Griff, verfügt über eine natürliche Geruchshemmung, eine antibakterielle Wirkung, Wärmekonservierung und antistatische Eigenschaften – und das alles ohne chemische Zusätze.
Die Faser Seawool wird bereits in der Modeindustrie verwendet. Erste Designs aus dem Garn sind käuflich erhältlich.